Dans le monde industriel, la performance des équipements dépend souvent de composants apparemment simples mais pourtant critiques. Parmi eux, les filtres jouent un rôle essentiel dans la protection des machines, la qualité des produits et l’efficacité énergétique. Pourtant, leur remplacement est souvent négligé ou effectué de manière réactive, entraînant des coûts inutiles, voire des pannes majeures. Savoir identifier les signaux d’alerte et comprendre les enjeux du changement de filtres permet aux entreprises de maintenir une production fluide, économique et durable.
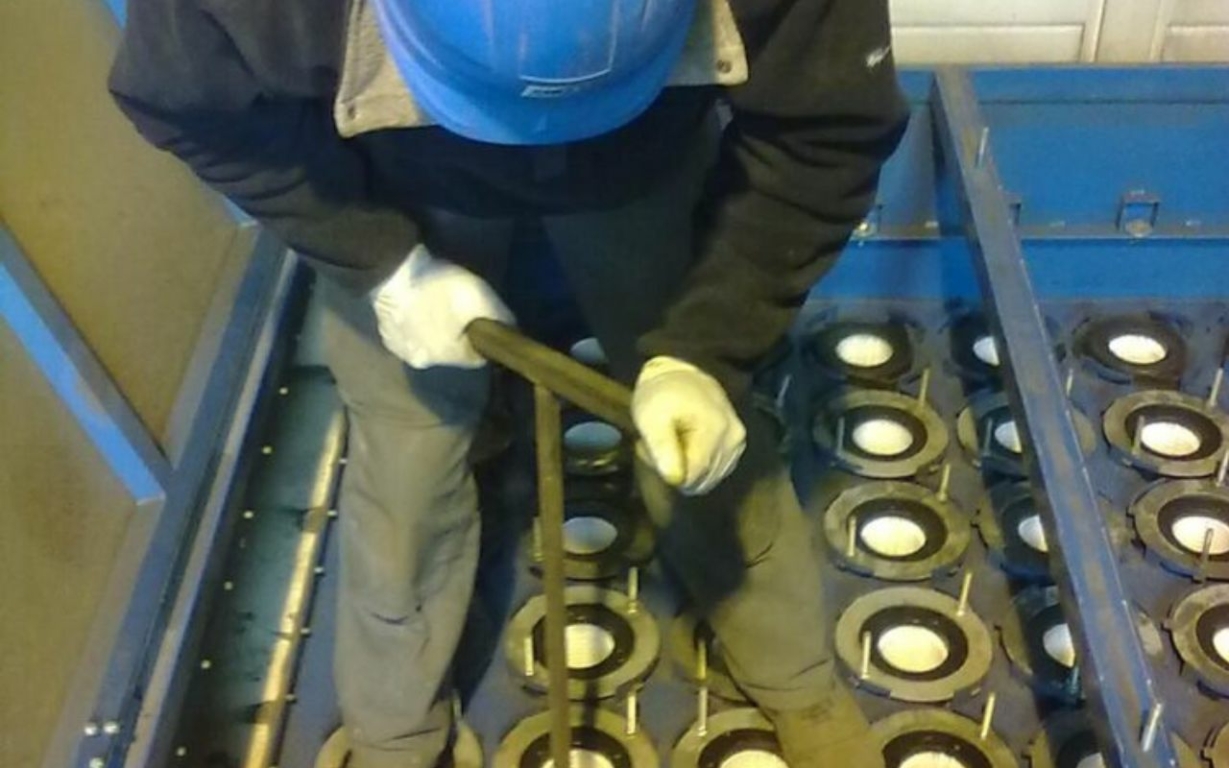
Sommaire
Signaux d’alerte et indicateurs de remplacement
La surveillance régulière des filtres industriels est bien plus qu’une simple routine technique. C’est une démarche stratégique visant à prévenir les défaillances avant qu’elles ne surviennent. Plusieurs indicateurs peuvent guider cette décision, allant de mesures précises à des observations visuelles ou même à l’analyse du comportement global du système.
Surveillance de la pression différentielle
L’un des paramètres les plus fiables pour juger de l’état d’un filtre est la pression différentielle, c’est-à-dire la différence de pression entre l’amont et l’aval du filtre. Lorsque cette valeur augmente, cela signifie que le filtre se colmate sous l’effet des particules captées. Ce phénomène réduit le débit du fluide et oblige les pompes à travailler davantage, ce qui accroît la consommation énergétique.
Les fabricants indiquent généralement un seuil limite au-delà duquel le filtre doit être remplacé ou nettoyé. Mais attention : ces chiffres sont indicatifs. Les conditions réelles d’utilisation — température, humidité, nature des contaminants — influencent aussi l’évolution de la pression différentielle. En outre, une légère augmentation prolongée peut avoir un impact financier non négligeable sur la facture énergétique.
Pour suivre cet indicateur en temps réel, il est conseillé d’installer des pressostats différentiels. Certains modèles sont capables de déclencher des alertes automatiques (visuelles, sonores ou intégrées à un système SCADA) lorsque le seuil critique est atteint. Cette solution apporte une véritable tranquillité d’esprit, surtout dans des environnements où la surveillance humaine est limitée.
Indicateurs visuels et physiques
Outre les mesures techniques, une inspection visuelle régulière reste un pilier de la maintenance. Elle permet de détecter des anomalies qu’un capteur pourrait manquer. Voici quelques points à surveiller attentivement :
- Déchirures, fissures ou trous dans le matériau filtrant.
- Affaissement ou déformation due à la pression ou à l’usure.
- Usure par frottement contre les parois ou autres éléments.
- Fuites autour du filtre pouvant indiquer un mauvais joint ou un montage incorrect.
- Joints endommagés ou usés, incapables d’assurer l’étanchéité.
Ces signes visibles doivent être pris au sérieux. Même une petite déchirure peut provoquer une contamination significative ou une baisse notable de performance.
Signes de performance dégradée
Parfois, le filtre n’est pas encore percé ni obstrué, mais son efficacité commence à chuter. Comment le savoir ? Tout simplement en observant le comportement global de l’équipement. Voici quelques symptômes révélateurs :
- Baisse de l’efficacité de filtration avec passage accru de contaminants.
- Augmentation de la consommation électrique ou hydraulique des machines associées.
- Bruits inhabituels pendant le fonctionnement, comme des vibrations ou des sifflements.
- Problèmes de séparation ou de flottabilité des fluides dans les systèmes concernés.
- Présence accrue de poussière ou impuretés dans l’environnement immédiat.
Ces signaux ne trompent pas. Ils montrent que le filtre a perdu une partie de sa capacité à protéger le système. Ignorer ces indices revient à jouer avec le risque.
Fréquences de remplacement recommandées
Si les indicateurs donnent des alertes précoces, les plannings de remplacement restent une référence utile, surtout pour anticiper les besoins logistiques et budgétaires. Toutefois, les intervalles varient fortement selon le type d’équipement, l’intensité d’utilisation et les conditions environnementales.
Approche basée sur l’utilisation
Une approche pragmatique consiste à aligner les fréquences de remplacement sur le temps d’utilisation. Voici un ordre d’idée couramment appliqué dans l’industrie :
- Petit entretien : toutes les 500 heures d’utilisation.
- Entretien intermédiaire : tous les 3 à 6 mois.
- Grand entretien : conformément aux spécifications du fabricant.
Cette méthode offre une base solide, mais elle doit toujours être ajustée en fonction des observations concrètes.
Fréquences spécifiques par type de filtre
Les différents types de filtres ont des durées de vie variables. Voici quelques repères généraux :
- Filtres HEPA et ULPA : entre 6 mois et 2 ans, selon la charge de pollution.
- Filtres à plis : tous les 3 à 6 mois, car ils se colmatent plus vite.
- Filtres à charbon actif : tous les 6 mois à 2 ans, en fonction de la concentration de contaminants.
- Filtres de protection respiratoire : selon un calendrier établi sur des critères objectifs (exposition, durée d’utilisation, etc.).
En somme, chaque application a ses exigences. Il est donc crucial de connaître les spécificités de votre équipement et de vous y tenir.
Considérations économiques
Le coût d’un filtre représente rarement une dépense majeure en soi. Ce sont plutôt les effets secondaires d’un filtre mal entretenu qui viennent peser sur le budget. Le défi consiste à trouver le bon équilibre entre dépenses immédiates et gains à long terme.
Un remplacement trop fréquent génère des coûts inutiles, des arrêts de production et une surconsommation de ressources. À l’inverse, attendre trop longtemps expose à des pannes coûteuses, une usure prématurée des machines et une baisse de qualité des produits. La clé est donc dans la précision du timing.
Conséquences des filtres défaillants
Impact sur la productivité
Un filtre mal choisi ou mal entretenu peut réduire la productivité de manière insidieuse. Par exemple, un filtre obstrué peut diminuer le débit de filtration de plus de 30 % tout en augmentant la consommation énergétique de 20 %. Cela semble peu, mais multiplié par des heures de fonctionnement quotidiennes, cela devient significatif.
Plus grave encore, un filtre endommagé peut céder brutalement, libérant des contaminants dans le système. Résultat : contamination massive, arrêt imprévu de la chaîne, ou perte irréversible de lots entiers de production.
Coûts des temps d’arrêt
Les temps d’arrêt liés à un filtre défectueux peuvent coûter extrêmement cher, surtout dans des secteurs ultra-sensibles. Voici quelques exemples concrets :
- Industrie automobile : jusqu’à 15 000 $ perdue par minute d’immobilisation.
- Industrie pharmaceutique : destruction totale de lots entiers, avec des pertes pouvant atteindre plusieurs centaines de milliers d’euros.
- Verrerie : entre 2 000 et 15 000 $ par heure de panne, selon la complexité du processus.
Ces chiffres parlent d’eux-mêmes. Un filtre mal géré peut rapidement devenir une source de pertes financières dramatiques.
Risques pour les équipements
Outre les conséquences économiques, les filtres défaillants mettent également les équipements en danger. Les dommages causés peuvent être multiples :
- Usure prématurée des cylindres (8 fois plus rapide), des pistons (3 fois plus).
- Contamination des circuits hydrauliques et pneumatiques.
- Obstruction des passages d’admission, réduisant la puissance disponible.
En d’autres termes, négliger les filtres revient à sacrifier la longévité des machines elles-mêmes.
Stratégies d’optimisation et maintenance préventive
Mise en place d’un programme préventif
Face à ces enjeux, la mise en place d’un programme de maintenance préventive structuré est indispensable. Il doit inclure :
- Des inspections programmées à intervalles réguliers.
- Une surveillance continue des paramètres clés (pression, débit, température).
- Des tests de fonctionnalité périodiques pour valider l’efficacité globale.
- La formation du personnel à la reconnaissance des signes d’alerte.
Ce type de stratégie permet de passer d’une gestion réactive à une approche proactive, évitant les surprises coûteuses.
Utilisation d’indicateurs de maintenance
Les technologies modernes offrent des solutions intelligentes pour simplifier la surveillance. On peut notamment compter sur :
- Indicateurs visuels colorés pour une lecture immédiate de l’état du filtre.
- Capteurs électriques envoyant des alertes automatisées dès qu’un seuil critique est franchi.
- Systèmes sans fil permettant une surveillance à distance.
- Intégration télématique pour une gestion centralisée du parc de filtres.
Investir dans ces outils facilite la prise de décision, améliore la traçabilité et réduit le risque humain.
Approche économique : analyse coût-bénéfice
Chaque décision de remplacement de filtres industriels doit s’appuyer sur une analyse coût-bénéfice globale. Celle-ci prend en compte :
- Le prix d’achat du filtre.
- Les coûts d’installation (main-d’œuvre, matériel spécifique).
- La durée de vie estimée du filtre.
- Les économies réalisées en termes de consommation énergétique ou de préservation des équipements.
- Le risque de temps d’arrêt imprévu.
En intégrant ces paramètres dans un modèle économique, il devient possible de déterminer le moment optimal pour effectuer le changement — ni trop tôt, ni trop tard.
Comment choisir ses fournisseurs et partenaires techniques ?
Face à la complexité des besoins en filtration industrielle, il est essentiel de s’entourer de partenaires compétents et réactifs. Le choix d’un fournisseur ne se limite pas à la qualité des produits proposés, mais englobe aussi des services annexes comme la livraison rapide, l’assistance technique ou encore la possibilité de régénération des filtres usagés.
Un partenaire sérieux comme SB Filtres & Techniques propose non seulement une large gamme de filtres adaptés à tous les environnements industriels, mais également une expertise terrain pour accompagner les entreprises dans leurs décisions. En effet, ce type de prestataire peut réaliser des audits de performance, recommander des solutions personnalisées, voire assurer directement les opérations de remplacement pour garantir une installation optimale.
Avantages d’une prestation clé en main
Faire appel à un expert pour la fourniture et le remplacement de filtres industriels présente plusieurs avantages :
- Simplicité logistique : un seul interlocuteur pour la commande, la livraison et l’installation.
- Rapidité d’intervention : disponibilité en urgence pour éviter les arrêts prolongés.
- Conformité et sécurité : installations réalisées par des techniciens formés et équipés.
- Économie à long terme : filtres mieux adaptés, donc plus durables et plus efficaces.
En somme, collaborer avec un prestataire spécialisé permet de gagner en agilité tout en maîtrisant les risques liés à la filtration.
Conclusion
Le remplacement stratégique des filtres industriels n’est pas une simple question de routine technique, mais bien un levier de performance globale. En détectant les signaux d’alerte précocement, en appliquant des fréquences de maintenance adaptées et en s’entourant des bons partenaires, les entreprises peuvent significativement améliorer leur productivité, leur rentabilité et leur conformité réglementaire.
Dans un monde industriel où chaque minute compte et chaque euro est compté, négliger la filtration revient à jouer avec le feu. Alors que les technologies évoluent et que les exigences de qualité et de durabilité augmentent, il devient impératif de repenser sa stratégie de gestion des filtres pour rester compétitif, responsable et résilient face aux défis futurs.