L’industrie métallurgique repose sur un ensemble de chaînes de valeur. Dans sa forme classique, cette chaîne va du tournage à la finition, en passant par le fraisage. Mais à l’heure actuelle où l’évolution technologique bat son plein, d’autres éléments viennent s’ajouter à cette chaîne de valeur. Dans cet article, découvrez les différentes étapes de transformation des métaux.
Sommaire
Étape 1 : le tournage des métaux
Le tournage est une technique d’usinage visant à retirer de la matière sur une pièce de forme cylindrique.
La différence entre une opération de tournage extérieur et une opération de tournage intérieur
On parle d’opération de tournage extérieur lorsque l’outil ne s’attaque qu’à la surface extérieure d’une pièce. On a généralement recours à cette technique dans les procédés suivants :
- le chanfreinage,
- le rainurage,
- le dressage.
En ce qui concerne l’opération de tournage intérieur, elle ne s’applique qu’à l’intérieur de la pièce. Elle englobe des procédés classiques, comme :
- l’alésage,
- le perçage,
- le pointage,
- le centrage.
Vous trouverez tous les composants dont vous aurez besoin auprès de TVI Groupe, une société spécialisée dans la transformation de métaux.
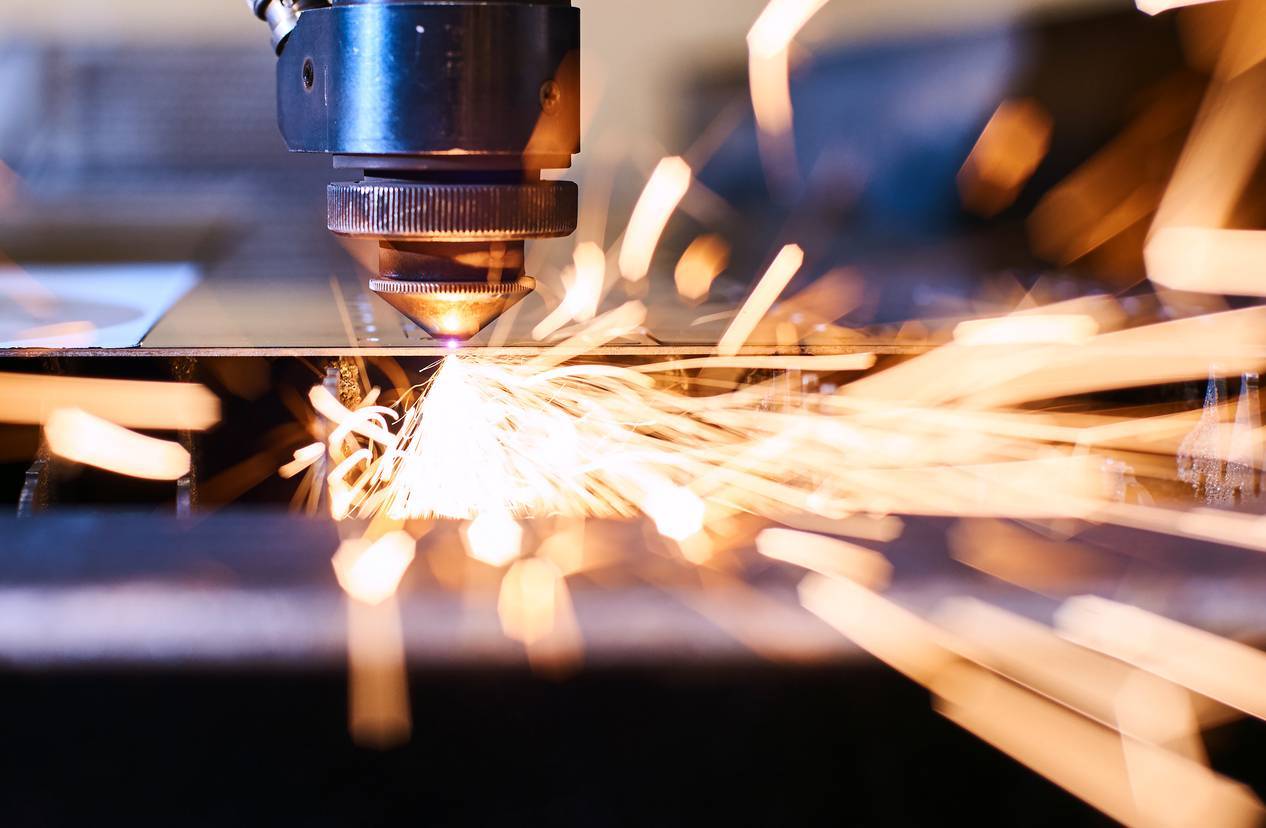
Le principe de fonctionnement du tournage de métaux
Pour réaliser des travaux de tournage, les industriels utilisent un outil bien spécifique : le tour. Pour l’utiliser, il faut procéder comme suit :
- placer la pièce dans le mandrin,
- se servir des mors pour serrer l’outil.
À noter que l’outil coupant est placé dans un porte-outil, que l’on appelle aussi la tourelle.
Pour s’adapter aux demandes les plus exigeantes, les tours offrent un large choix de déclinaisons. Sur le marché actuel, vous trouverez notamment des tours conventionnels qui doivent impérativement être contrôlés par un opérateur. Il existe aussi des tours automatiques qui ne nécessitent guère l’intervention d’un opérateur.
Pour ce qui est du tour CNC, une programmation automatique ou manuelle va prendre en charge toutes les opérations.
Étape 2 : le fraisage
Le fraisage fait partie des étapes de transformation de métaux les plus importantes.
Qu’est-ce qu’on entend par fraisage ?
D’une manière très simple, le fraisage consiste à découper les métaux afin d’obtenir des pièces mécaniques de haute précision. Pour ce faire, on utilisera une fraiseuse. Grâce à son cutter interchangeable, cette dernière est parfaitement capable de réaliser différentes sortes de coupe.
Toutefois, pour extraire les couteaux du métal lors du fraisage, vous devrez vous servir de petites roues dentées, aussi appelées fraises.
Comment utilise-t-on la commande numérique CNC pendant le fraisage ?
À l’heure actuelle, la technique de fraisage par ordinateur CNC reste de loin la plus efficace. La raison est simple : les robots assurent une meilleure précision que l’être humain. Un point très crucial dans un processus d’usinage.
Le fraisage par ordinateur CNC propose un fonctionnement simple basé sur le système de coordination contrôlé par ordinateur. En effet, les opérateurs ont le choix entre :
- le logiciel FAO (fabrication assistée par ordinateur),
- le logiciel de programmation automatique de CAO (conception assistée par ordinateur).
Selon la machine de fraisage utilisée, elle peut mouler une sphère métallique en utilisant des mouvements de 3 à 5 axes.
Avec la fraiseuse par assistance numérique, plusieurs types de fraisage sont possibles. On cite notamment :
- le fraisage par coupe,
- le rainurage droit,
- le rainurage de forme.
Étape 3 : la finition des pièces métalliques
Il existe plusieurs types de finitions des pièces métalliques, en fonction de leur utilisation et de l’aspect recherché. Tout d’abord, il a la finition par marquage qui utilise différentes technologies. Le laser, la micro-percussion et le rayage en font partie. Ces techniques facilitent l’identification du produit ainsi que son traçage. Elles permettant également de graver des informations sur l’origine et le fabricant de la pièce.
Quant à la finition par rodage, elle consiste à donner un aspect rugueux à la pièce mécanique. Dans le secteur automobile, on utilise généralement le système de rodage cylindre.
La rectification de finition, elle, est une opération d’usinage qui a pour objectif d’obtenir un état de surface de qualité. Pendant ce processus, l’utilisation d’une meule va ainsi enlever les copeaux fins pour obtenir des surfaces précises. Enfin, la tribofinition va modifier l’état des surfaces ainsi que les arêtes des pièces en métal.
Étape 4 : la gestion de sous-traitance
La gestion de sous-traitance touche de nombreux domaines. En premier, on cite le traitement thermique qui consiste à faire subir au matériau des transformations de structure. C’est une opération qui va améliorer les caractéristiques des pièces mécaniques. Elle permet notamment d’améliorer la résistance de l’acier.
Le traitement de surface, quant à lui, donnera aux pièces un aspect visuel ou technique répondant aux besoins des industriels. Beaucoup considèrent ce procédé comme étant une opération mécanique ou chimique.
Enfin, le taillage est une opération d’usinage visant à enlever un surplus de matière d’une pièce métallique. À noter que ces différentes opérations doivent faire l’objet d’une gestion spécifique par des professionnels.
Étape 5 : le contrôle
Dans le secteur de la métallurgie, la qualité revêt une grande importance. C’est pour cela qu’on accorde un intérêt particulier à l’étape de contrôle. La maitrise des risques étant importante, les contrôles non destructifs doivent être mis en œuvre. Le contrôle CND peut se faire par ultrason sur une pièce qui vient de sortir de la chaîne de fabrication. Après l’usinage de la pièce, le contrôle peut se faire par magnétoscopie ou ressuage.
Le contrôle haute précision 3d ou tridimensionnel, lui, est réservée aux pièces les plus complexes, notamment aux pièces des prothèses articulaires. L’équipement le plus utilisé étant la machine de mesure tridimensionnelle (MMT). Les capteurs vidéo peuvent également remplir cette fonction.
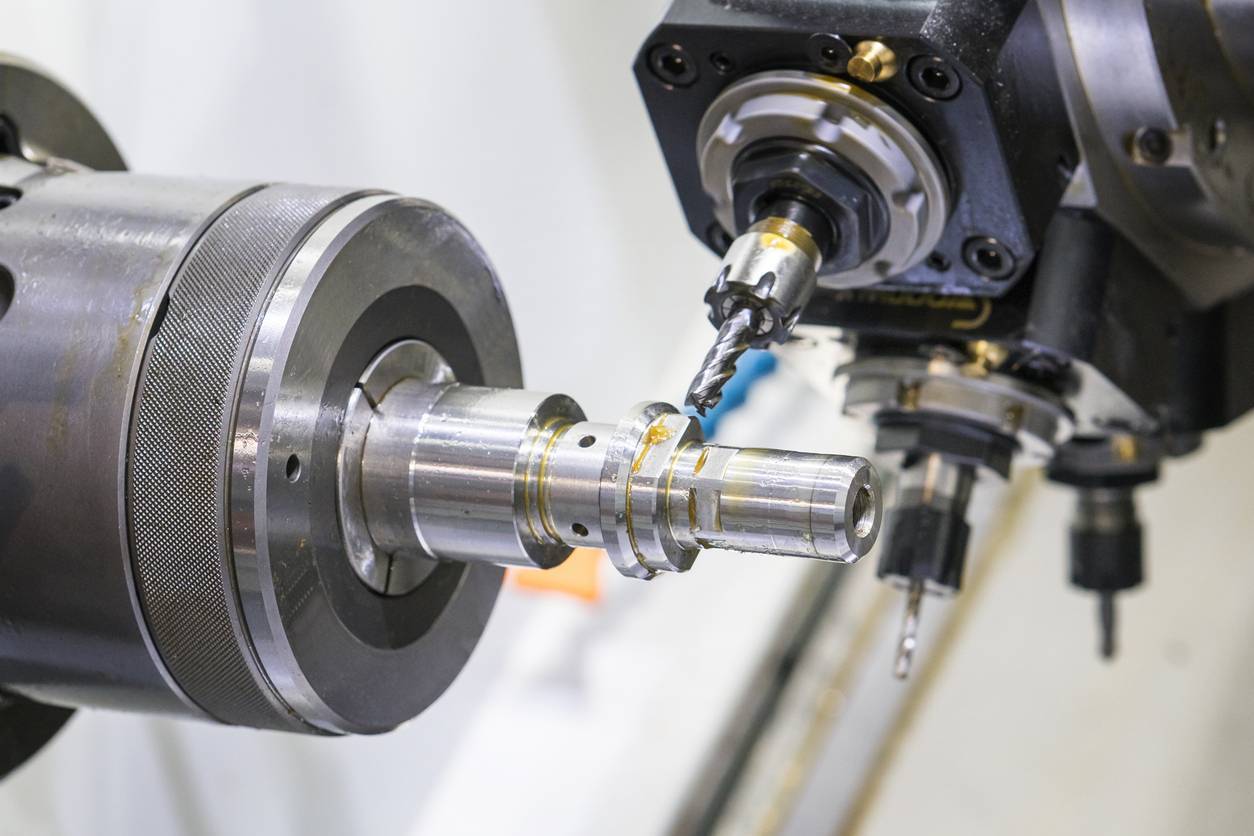
Étape 6 : l’assemblage
Après la transformation des matières premières et la fabrication des pièces, la dernière étape de la production consiste à assembler les produits finis. Elle peut faire appel à la technique de sous-ensemble ou d’assemblage mécanique. Cette dernière fait appel à un savoir particulier qui nécessite une technologie variée. Il peut s’agir de la soudure, du collage ou d’un montage de précision.
L’assemblage des produits finis devrait être fait dans un espace dédié différent de celui de l’usinage des pièces métalliques. Les lignes d’assemblage pouvant ainsi être manuelles ou automatiques.